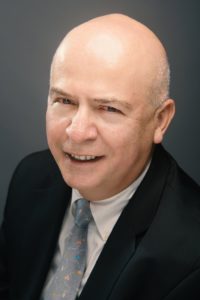
What do navy ships and Hollywood movies have in common? More than you might think, in the eyes of Bahadir Inozu, MSE, PhD, at least. Inozu got his start managing engineering projects for naval ships, then applied that knowledge across a surprisingly wide variety of industries. His ability to think creatively about the applications of project management techniques helped him transform health care, government — and yes, even film. In his latest endeavor, Sharp Focus, Inozu is helping to engineer the movie production process, from script to screen.
For each industry, Inozu brings thoroughly new ways of seeing, based on key principles. And some of his solutions are deceptively simple. “I can show you, today, how to increase your capacity just by single-tasking,” he explains. For a big IT project, he says, the primary achievement was to avoid task-switching — and it nearly doubled productivity, in just two months. “You can start doing that tomorrow,” Inozu explains. “People just don’t know about it.”
As an author — as well as an educator and business executive — that lack of knowledge is the bottleneck he’s trying to fix.
How do naval architecture and marine engineering connect with project management?
I started managing research projects first. At the University of New Orleans, we started developing software that is related to reliability management of ship machinery. That was a pretty large software development for an international project, designed to work on multiple platforms.
Agile methodology wasn’t known at that time. I had been working with ship operators and classification societies. They kept changing specs on me. Each user had a different system on their ships and on shoreside — some were in Japanese. It was my first exposure to really tough IT project management. And I learned a lot.
And how did you transition from that to, say, health care — the topic of one of your books?
We were combining process improvement techniques for Naval Aviation Enterprise: Theory of Constraints (TOC), Lean and Six Sigma. That body of knowledge, applied in that way to aircraft maintenance, was pioneering.
It started as a process improvement for supply chain management for the aircraft on board the carriers. However, based on our experience of integrating these leading methods, we realized that we could integrate an application of TOC, called Critical Chain Project Management with Lean, Agile and some other techniques to improve project management. That was an interesting milestone for me.
We ended up implementing the approach for the state of Utah — and we got some amazing results. We were able to double the IT throughput in two months— to more than fivefold within a year. I’m always looking for opportunities to use this really new, powerful, innovative technique in other industries, including construction, even entertainment.
How does project management apply to entertainment?
A lot of movies are finished behind schedule and over budget. Very frequent change in scope is considered normal. With these new techniques, in those environments, the impact of dynamic changes can be mitigated effectively to increase the profitability of the production while keeping the creative teams happy.
It’s really the evolution of my exposure to different industries. I’m a mechanical engineer, that’s how I started. Then I got my graduate degrees in Naval Architecture and Marine Engineering. We started applying best of the breed process improvement techniques such as Lean Six Sigma to ship production and design. Then to naval aviation. Then came the major transformation — healthcare. Then we expanded into manufacturing processes as well as government processes — the Department of Defense, federal government, state governments. These methodologies are applicable across the board.
What are some of the similarities, across industries?
I’ve had the opportunity to work with over 40 organizations in multiple industries. There is one area where you have a permanent constraint: you can never get enough from IT. The demands on IT departments exceed their capacity three to five times, they can never do enough. Research and development is another one. Research projects by definition have challenges in terms of managing scope. We have powerful techniques to manage that.
What would you say is your area of expertise?
Three areas. The first one is acceleration with staggering, better management of uncertainty with buffers and other strategies. We have been developing and enhancing buffer management, in terms of managing time, scope and cost. That is a very effective technique that more and more organizations are using.
The second one is focusing on your key leverage points to get the highest ROI from projects. I was amazed to see how many executives don’t see projects as investments. That’s why my new company is called “Sharp Focus.” Sometimes there can be a great premium for speeding up projects. If you finish a hotel two months early, you can start renting those rooms early.
Then there’s risk management. High reliability organizations (HROs) — the topic of my latest book — is another method that is in its infancy in project management. You need to be preoccupied with failure. It’s a very dynamic world out there. The HRO framework has proven to be very effective in high risk environments. It has been widely applied in aviation, the air-traffic-control system, nuclear power industry, wildfire fighting and recently healthcare.
I am very motivated to bring these performance and process improvement techniques to class. Theory of Constraints changed my life.
When did you first learn about TOC?
Well, you make a plan and then nature takes over.
After Hurricane Katrina, we got a very big contract from the Navy. It was an amazing and huge project, involving over 50 naval bases around the world. I ended up leaving my job security [in a tenured position at the University of New Orleans], and jumped into this super exciting but very high risk opportunity with NOVACES [the company Inozu co-founded]. NOVACES became one of the fastest growing companies in the U.S. It was on the Inc. Magazine list for two years in a row.
What I saw, after managing change and a lot of process improvement projects, was that we needed to implement it to project management. When we were integrating Lean and Six Sigma for Naval Ship Design and Production, one of the Northrop Grumman executives gave me a copy of Critical Chain by Eliyahu Goldratt, Father of TOC. That’s how I first learned about TOC. Critical Chain can double the speed of a project with 30% cost savings. As we got into the details, as things were evolving, we realized we can take the best strategy and tactics from other methods and get even better results. Agile is great when scope keeps changing. Critical Chain is great to manage uncertainty. I love thinking out of the box to integrate these methods, enabling me to get some amazing results.
How did all of this change the way you work?
The moment you introduce some radical changes to the way you do things, you get a lot of resistance. In Critical Chain, you don’t have milestones at the task level, you have a task, and you work on the task as fast as you can as if you are in a relay race. I mentioned this to a seasoned project manager in Utah. He said, “For 30 years, I’ve managed with milestones — I’m not changing.”
The State of Utah is unique. The governor promised 25% measurable improvement across all government agencies. And they delivered ahead of time. That required very careful change management. Not everyone likes change, so it’s about managing that change, showing people what’s in it for them, listening to them. In project management work, it’s all about communication. I tell students, there are three secrets to project management success — communication, communication, and communication.
I noticed you produced a documentary last year. Could you talk a bit about that experience?
I am passionate about adapting proven, “best of breed” tools and methods to film production. So, independent filmmaker James Lester invited me to join the team of his latest documentary project, which was starting its post-production in 2016. It allowed me to understand the challenges of independent film production and introduce some of the techniques to use the resources more effectively as an Executive Producer.
When you are not bringing TOC to new industries, what do you enjoy doing?
As far as hobbies are concerned, I like photography and going to the movies but I also love traveling around the world and experiencing different cultures.
What are you looking forward to most about teaching Principles of Project Management?
Theory of Constraints, which is looking at the big picture and figuring out your main constraints, your bottlenecks. Once you take a look at your constraining resources, you figure out a way to get the most out of your bottlenecks.
There is a well-established roadmap, even for organizations like Boeing, for instance, which was able to speed up projects tenfold by implementing the principles of TOC. And it’s not just TOC — I’m not a zealot. We keep adding more methods and technologies as they are invented. We have AI. We have Big Data Analytics. All of these improvements depend on making changes in process, people and technology.
The tools are available. I love teaching them and make the world a better place — one project or portfolio at a time.
Professor Bahadir Inozu teaches PJMT 500: Principles of Project Management.
This interview has been edited for length and clarity.